What is Porosity in Welding: Comprehending Its Reasons and Enhancing Your Skills
Wiki Article
Recognizing Porosity in Welding: Discovering Reasons, Effects, and Prevention Strategies
Porosity in welding is a persistent difficulty that can considerably affect the top quality and stability of welds. As professionals in the welding market are aware, understanding the reasons, results, and prevention strategies connected to porosity is crucial for accomplishing durable and reputable welds. By diving right into the origin triggers of porosity, analyzing its detrimental effects on weld quality, and exploring reliable avoidance strategies, welders can boost their understanding and abilities to generate high-quality welds regularly. The complex interaction of variables adding to porosity requires a detailed understanding and an aggressive technique to make certain successful welding end results.Common Sources Of Porosity
Contamination, in the kind of dust, grease, or rust on the welding surface, produces gas pockets when heated, leading to porosity in the weld. Inappropriate protecting occurs when the shielding gas, frequently made use of in processes like MIG and TIG welding, is incapable to completely secure the molten weld pool from reacting with the surrounding air, resulting in gas entrapment and succeeding porosity. In addition, poor gas protection, often due to inaccurate circulation rates or nozzle positioning, can leave parts of the weld unprotected, enabling porosity to develop.Results on Weld Top Quality
The presence of porosity in a weld can substantially compromise the general top quality and stability of the bonded joint. Porosity within a weld produces spaces or dental caries that compromise the structure, making it much more prone to splitting, deterioration, and mechanical failing. These gaps serve as anxiety concentrators, minimizing the load-bearing capacity of the weld and boosting the probability of early failure under used tension. Additionally, porosity can likewise offer as prospective sites for hydrogen entrapment, further aggravating the deterioration of the weld's mechanical residential properties.In addition, porosity can prevent the performance of non-destructive testing (NDT) techniques, making it testing to identify various other problems or suspensions within the weld. This can lead to significant safety and security problems, particularly in crucial applications where the structural honesty of the bonded parts is paramount.
Avoidance Techniques Summary
Provided the detrimental effect of porosity on weld quality, efficient prevention strategies are crucial to preserving the architectural stability of welded joints. Among the primary prevention strategies is detailed cleansing of the base materials before welding. Impurities such as oil, oil, corrosion, and dampness can add to porosity, so ensuring a clean work surface is essential. Appropriate storage of welding consumables link in completely dry conditions is likewise crucial to stop wetness absorption, which can result in gas entrapment during welding. Additionally, picking the proper welding specifications, such as voltage, current, and take a trip rate, can assist reduce the danger of porosity development. Ensuring ample shielding gas flow and coverage is an additional essential prevention method, as inadequate gas coverage can cause atmospheric contamination and porosity. Appropriate welder training and accreditation are necessary for carrying out precautionary procedures successfully and constantly. By integrating these prevention methods into welding practices, the occurrence of porosity can be significantly reduced, leading to more powerful and a lot more trustworthy bonded joints.Relevance of Appropriate Protecting
Appropriate securing in welding plays an important role in protecting against atmospheric contamination and ensuring the stability of bonded joints. Protecting gases, such as argon, helium, or a combination of both, are typically made use of to safeguard the weld swimming pool from reacting with aspects airborne like oxygen and nitrogen. When these reactive elements enter into contact with the hot weld swimming pool, they can cause porosity, resulting in weak welds with lowered mechanical residential properties.
Poor securing can cause numerous issues like porosity, spatter, and oxidation, endangering the architectural honesty of the welded joint. Therefore, sticking to appropriate shielding practices is vital to generate top notch welds with marginal problems and ensure the longevity and integrity of the bonded elements (What is Porosity).
Tracking and Control Methods
Just how can welders successfully keep track of and regulate the welding next page procedure to ensure optimum results and protect against flaws like porosity? One key approach is through the usage of sophisticated monitoring innovations. These can include real-time tracking systems that provide responses on parameters such as voltage, present, travel speed, and gas circulation rates. By continually keeping track of these variables, welders can recognize discrepancies from the excellent conditions and make instant adjustments to avoid porosity formation.
Furthermore, applying proper training programs for welders is vital for checking and regulating the welding process effectively. What is Porosity. Informing welders on the importance of maintaining regular parameters, such as correct gas securing and travel rate, can assist protect against porosity concerns. Routine evaluations and accreditations can also make certain that welders are efficient in tracking and controlling welding procedures
Moreover, using automated welding systems can improve surveillance and control abilities. These systems can precisely manage welding parameters, reducing the possibility of human mistake and making certain regular weld high quality. By incorporating sophisticated monitoring modern technologies, training programs, and automated systems, welders can successfully check and regulate the welding procedure to reduce porosity issues and accomplish high-quality welds.
Final Thought
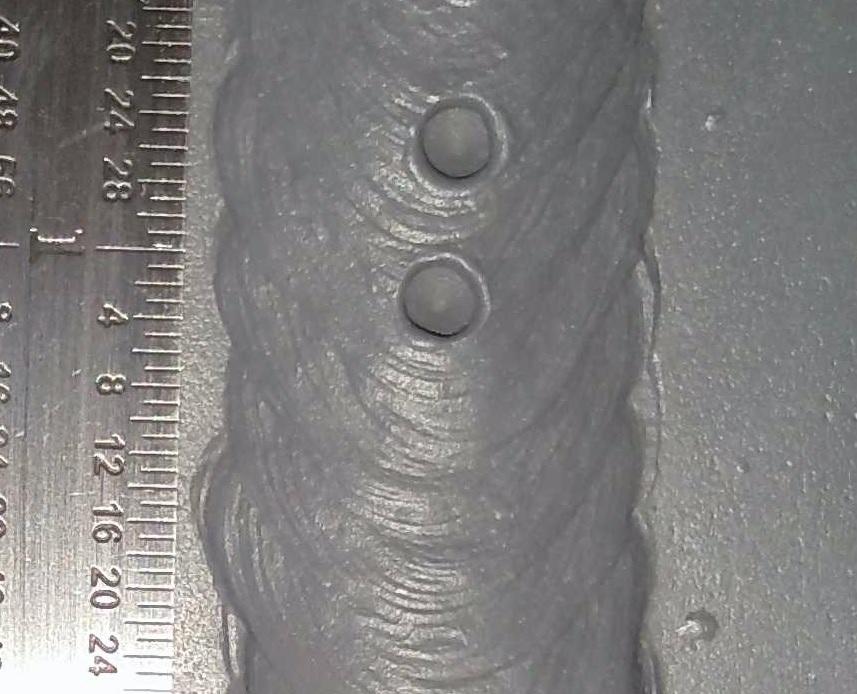
Report this wiki page